出荷作業のよくある課題
出荷作業とは、受注などを受けて出荷指示のあった商品の在庫を確認することから、ピッキング、検品、納品書・領収書などの書類の発行、梱包、発送手配、トラックへの積み込みまでの一連の作業を指します。
出荷業務は商品を倉庫から出す最終段階の重要な業務ですが、ミスが発生しやすく、生産性が落ちやすい工程でもあります。このことから、現場ではよく次のような課題に直面しています。
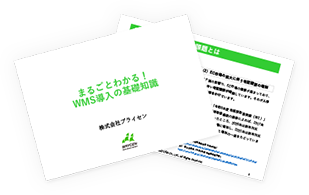
よくある課題
ピッキング時にミスが多発する
ピッキングの際に、商品の数量、カラー、サイズなどの取り間違いのミスが頻発するという課題です。人が目視で行っている場合はどうしてもヒューマンエラーが起こってしまいます。
【関連コラム】
倉庫内の検品ミスを減らすには?対策方法を解説します!
検品・梱包時にミスが多発する
検品・梱包の際には、セット品や景品の封入漏れ、伝票や納品書の取り間違い、宛先ラベルの貼り間違いなどのミスが起こります。また作業工程に無駄があり、非効率的であることから出荷指示からのリードタイムが長引いてしまうといった課題もあります。
データ管理の時点のミスが多発する・管理が煩雑になっている
出荷作業を開始する前のデータ管理の時点で課題が生じることもあります。
普段から在庫管理が正確にできておらず、出荷する際にも在庫を引き当てられないというケースや、在庫管理そのものが煩雑で負荷が大きいという課題もあります。
出荷作業を効率化するメリット
上記のような課題を解決し、出荷作業を効率化するには一定のコストもかかるため後回しになりがちです。ここからは出荷作業を効率化することで得られるメリットをご紹介します。
1. コスト削減
出荷作業の効率化により作業時間が短縮されるため、人件費の削減に繋がります。
また在庫の回転率が向上することで、在庫管理コストも低減します。
2. 顧客満足度の向上
出荷作業を効率化することで、納期が短縮され、顧客に商品が早く届くため、
顧客満足度の向上が実現できます。
3. 作業スタッフの安全性の向上
出荷作業の効率化のために自動化技術やITシステムを導入することで、作業者に負担がかかる業務が減少し、安全性が向上します。
4. 保管効率の向上
効率的な出荷作業により、倉庫内のスペースがより有効に使われるため、倉庫を拡大する必要がなくなったり、ロケーション管理がしやすくなり作業効率がアップします。
5. 競争力の向上
出荷作業の効率化により、他社よりも迅速かつ正確なサービスを提供できるため、企業としての競争力が向上します。
このように、出荷作業の効率化はコストはかかりますが、大きなメリットも生み出すのです。
出荷業務の改善フロー
出荷作業効率化のための出荷業務の改善は、やみくもに行っても効果が出にくいため、適切な手順を踏む必要があります。ここでは、効率化に必要な改善のフローを紹介します。
1.現状分析
まず、出荷業務の現状分析から始めます。作業に関わっているメンバーで出荷工程を洗い出し、無駄な業務フローがないかをチェックします。また、作業場所や道具に問題はないか、必要以上に時間や手間がかかる業務はどこか、どの工程でミスが起きやすいのか、その出荷ミスの原因はどこにあるのか、などの問題になっている要因を特定します。また、スタッフの作業負荷が高すぎる業務がないか、という点もチェックします。
2.改善策の検討
次に改善策を検討します。ミスを減らすためのチェック体制の見直しや、マニュアルの整備、業務効率化のためのシステム導入などの具体的な改善策を検討します。出荷業務の改善は、作業速度だけでなく品質向上も大切です。改善策の検討にあたっては品質が疎かになっていないか、という点も注意しましょう。
3.施策の実行
次に改善策を実行します。新たな業務フローやシステムを導入します。初期段階では混乱が生じることや、スタッフから不満が出る可能性もありますので、事前のアナウンスや、目的をしっかりと説明しましょう。
4.効果検証
最後に、改善効果の検証を行います。改善を行った結果、実際の出荷業務の作業時間がどれだけ効率化できたか、品質がどのように変わったかを定量的・定性的に評価します。そのデータを活用しに、さらなる改善策を考えることで、継続的な改善を進めていきます
出荷作業の課題解決策
上記の課題を受け、出荷作業におけるそれぞれの工程ごとの解決策をご紹介します。
ピッキング
ピッキングにおいては、オーダーピッキングとトータルピッキングを使い分けることや、ハンディターミナルによるピッキングを検討することなどが考えられます。
・オーダーピッキング(摘み取り方式)
一つの発送先の出荷指示があるたびに、ピッキングする方式です。基本的に一人で作業を行えます。一つ一つの出荷作業はシンプルで簡単ですが、出荷指示が多いと効率がよくありません。
・トータルピッキング (種まき方式)
出荷指示がある前に、複数の発送先の商品をまとめてピッキングしておき、出荷指示があったときに荷さばき場で発送先ごとに分ける方法です。
ピッキング回数が少ないことがメリットとなります。特に同じ商品の組み合わせが多いときに効果を発揮します。一方で、仕分け作業を要するため、時間がかかることがあります。
・ハンディターミナルによるピッキング
ハンディターミナルとは片手で持てるハンディサイズの作業端末です。事前にハンディターミナルと連携するシステムに商品とロケーションを登録しておき、出荷指示書の商品ごとにロケーション情報が盛り込まれたバーコードを記載しておきます。
作業者は出荷指示があるごとにハンディターミナルでバーコードを読み込むだけで、品物の情報と正確な位置を知ることができます。そして棚に行き、ピッキングする際に商品のバーコードを読み取ることで、同時に検品もできます。
また作業動線を見直し、時間短縮のために移動がしやすい状態を作ることも重要です。動線に不要な荷物が置かれていたり、道幅が十分に確保されていなかったりして非効率的になっている状態を排除します。
検品・梱包
ハンディーターミナルによる検品を行い、検品をデータ照合によって行うことで、ヒューマンエラーを防ぐことができます。
また自動梱包機を導入することで梱包自動化につながります。
作業動線の見直しは検品・梱包工程でも有効です。
データ管理
WMS(倉庫管理システム)や在庫管理システムの導入によって在庫情報や人員配置、設備などの倉庫内作業に関するあらゆるデータによる可視化を行います。これにより、リアルタイムで倉庫内が把握できるようになるため、倉庫内作業全般をデータに基づいて行うことができます。全体の作業のヒューマンエラーを削減できるので、スピードアップにもつながります。
出荷作業を含めた倉庫内作業全体
出荷作業を含めた倉庫内作業全体の効率化のために、業務の標準化を目的としたマニュアル化を行ったり、倉庫内整理を徹底することで作業効率を高めたり、作業スタッフを増員したり、アウトソーシングを利用したりする方法もあります。
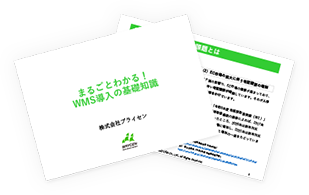
出荷作業の効率化に成功した事例
システム導入により、出荷作業を効率化した事例をご紹介します。
WMS一本化により出荷開始時間を2時間早められた
ある化粧品メーカーは、複数のWMSを導入していましたが、在庫管理や拠点間の連携に時間と労力がかかることに課題を感じていました、そこで効率の良いWMSに一本化したところ、毎朝7時になると自動的に出荷指示のデータが連携できるようになったので、出荷の開始時間を従来から2時間も早めることができました。また季節ごと、お客様ごとに変わる20枚ほどの同梱物を効率的に管理できるようになり、出荷作業が大幅に改善できました。
物流画像検品システムで出荷作業の生産性が1.7倍に向上
ある倉庫業を営む会社は、顧客である通販事業者が持つ「発送先ごとに同梱物を差別化したい」などのニーズへ柔軟に応えるために、WMSと連携させることで自動検品が可能な物流画像検品システムを導入しました。
作業スタッフが検品レーンに商品を乗せるだけで、検品から梱包まで自動で行うことができる仕組みです。結果、1時間あたりの作業数が280個だったところ、システムの導入で500個となり、出荷量が1.7倍に増えました。同じ出荷量で比較すると、人員は3人減を実現しました。
まとめ
出荷作業は、倉庫内業務の中でも最終段階である重要な工程であることから、ミスの削減やリードタイム短縮化、作業効率化が重要になってきます。各種課題を解決するために有効になるのが、WMSの導入です。
ブライセンのWMSである「COOOLa」は、ソフトウェア開発のプロフェッショナルである弊社が、豊富な物流業界の支援の中で培ったノウハウを最大限に活かして開発したクラウド型倉庫管理システムです。
現場スタッフの利便性を考えた豊富な機能と使いやすい操作性をご提供すると共に、お客様ごとに最適な機能を提供できるよう、カスタマイズも柔軟かつスピーディに提供します。
出荷作業の効率化にもお役立ていただけるようサポートいたしますので、ぜひお気軽にご相談ください。