効率化が求められる物流業界
日本ではどこの業界も人手不足が生じています。なかでも物流業界は特に人手不足が深刻化しており現場の従業員の数は年々減少しているのが現状です。人手不足にも関わらず、コロナウイルスの流行などのきっかけに通販需要の拡大が生じて物流件数は増加し続けています。そのような状況で少ない人数でより多くの物流件数に対応する為にシステム導入やオペレーションの改善に取り組んで物流業務の効率化を進めている企業も増えています。その中でもWMSを活用した倉庫内作業を行っている企業が増えてきています。
入荷作業・出荷作業の課題とは
効率性と正確性が求められている物流業界ですが、中でも入荷作業・出荷作業に関してはどのような課題があるのでしょうか。多くの企業が抱えている代表的な課題をご紹介いたします。
入荷作業の課題
・入荷作業に時間がかかる
入荷作業では、商品の検品や数量確認などが必要ですが、これらが手作業で行われている場合、多くの時間がかかるだけでなく、ヒューマンエラーも頻発してしまいます。
・ロケーション管理の最適化
入荷した商品を保管するスペースの不足や、保管位置が適切でないと、作業が滞りや効率化を妨げる原因となります。変わりつづける商品・在庫数を把握して常に適切なロケーション管理を維持する必要があります。
・情報のリアルタイム更新
入荷情報がリアルタイムでシステムに反映されていないことで、在庫数が足りず顧客のクレームになってしまったり、キャンセルに気付かず余剰在庫を生んでしまう可能性があります。
出荷作業の課題
・ピッキング作業の効率化が必要
出荷作業では、倉庫内から商品をピッキングする作業が多くの工数を占めます。ピッキングリストの最適化や、ピッキングルートの効率化が求められています。
・業務の標準化
これは出荷作業に限りませんが、ピッキング、検品、梱包などの業務は経験によってスキルのばらつきが生じやすく、速度や品質に差が出やすいです。そのため、業務を標準化し属人性を無くすことで、全体の効率化を図る必要があります。
・リードタイムの短縮
物流量が増加し続け顧客ニーズも高まる中、注文から配送までのリードタイムを短縮することが、顧客満足度の向上における重要な要素の一つになっています。
WMSとは
WMSは“Warehouse Management System“の略で日本では“倉庫管理システム”と呼ばれるシステムの事です。荷物が倉庫に入ってくる入庫から、どこに何があるのかロケーション管理、荷物が倉庫から出ていく出庫までをトータルで管理できるツールです。
>WMS(倉庫管理システム)とは?機能や物流倉庫に導入するメリットまで徹底解説
入荷作業をWMSで効率化する方法
取引先から送られてくる入荷予定情報をWMSに登録をします。この作業はCSVデータを介して登録するか、基幹システム(ERPなど)とWMSをAPI連携して自動で入荷情報を一括登録します。入荷予定リストが無い場合でも手動で情報登録をすることができるので急に発生した入荷予定の無い入荷に関しても対応が可能です。
実際に倉庫に荷物が届いたら入荷予定リストと届いた荷物の照合をハンディターミナルなどで行います。ハンディターミナルを使ってバーコードを読み取るだけでWMS内の在庫状況が約2秒程度で反映されるのでリアルタイムで在庫状況を追うことが可能です。
従来の手作業ではExcelなどで作成したリストを片手に確認作業を手作業で業務を行っていた為、ヒューマンエラーが発生したり、リアルタイムでの在庫状況が反映されなかったりと入荷作業以外にも時間を取られるケースが発生していましたがWMSを活用することで作業時間を半分以下に減らすことができたという事例もあります。また入荷予定リストと異なる商品が届いてしまった場合、バーコードをスキャンした段階でアラートが表示されるので誤入荷を防ぐことも可能です。
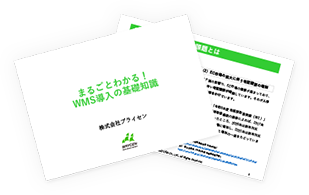
出荷作業をWMSで効率化する方法
出荷作業は受注管理システムやECサイトから受注情報(商品名、数量、顧客情報、希望納期)をWMSに連携し、WMSは受け取った受注情報を基に出荷指示を作成します。出荷指示書には、出荷対象品の詳細やロケーション、数量、配送先などの情報が記載されます。このタイミングでWMSが自動的に在庫を引当て、出荷可能な商品なのかを確認します。
出荷可能であればWMSは倉庫内の現場担当者に対して、どのロケーションからどのアイテムをピッキングするか指示を出します。ピッキングの指示に関してはシングルピッキング(摘み取り式)、トータルピッキング(種まき方式)どちらの対応も可能となっています。
現場担当者はWMSから出されたピッキングの指示通りに作業を行っていきます。
この際にハンディターミナルを活用し、商品やロケーションのバーコードをスキャンすることでピッキング指示された商品と一致しているか確認することが出来るので商品を間違えてピッキングすることを防ぎ、再ピッキングする手間を防ぐことができます。
実際にWMSを導入してからピッキング間違いに関してはほぼ0になったなどの事例もあります。トータルピッキングの場合、仕分け作業が発生しますがここでもWMSからリストを抽出することができるのでリストに従って出荷先ごとに荷物を仕分けすることも可能です。また現場担当者の声として多いのがピッキングする商品を事細かに目視で確認していた作業が無くなり負担がとても軽くなったという意見もあります。
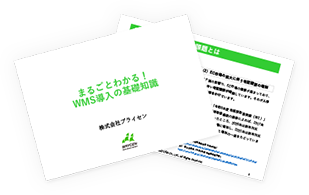
まとめ
入出荷(庫)作業は、倉庫内作業の中でも重要な作業の一つです。
入荷作業をミスすると在庫差異が生じてしまい、棚卸に時間が余計にかかってしまう、
出荷指示が出た際に必要な商品の用意が出来ないなどの原因となります。
同様に出荷作業をミスすると、お客様の注文と異なる商品を発送してしまいトラブルなどを招いてしまう原因となります。
入出荷(庫)作業でミスをなくすためにも、WMSとハンディターミナルを使用した検品を推奨しています。ブライセンのクラウド型倉庫管理システム「COOOLa」は、物流・倉庫業務の生産性を徹底的に追求した倉庫管理システムです。柔軟なカスタマイズ性と手厚いサポートを備えていることから、貴社にとって最適な倉庫管理を実現できます。ハンディターミナルによる検品機能もあるため、検品ミスの削減に寄与します。
倉庫内作業の検品に関する業務効率化にお悩みの方は、ぜひお気軽にご相談ください。