倉庫の出荷作業とは
倉庫業務における出荷作業とは、お客様から注文があった商品を、倉庫から発送するまでの業務のことです。出荷作業の業務フローには出荷指示、在庫引当、ピッキング、検品、梱包、発送という工程があり、すべてお客様の元に商品を届けるための重要な作業です。そのため、スピードを上げるための効率化や、誤発送などの大きなミスに繋がりやすい発送作業などの品質や精度を担保するためのマニュアル整備などが重要です。
倉庫の出荷作業の重要性
倉庫の出荷作業は顧客との信頼につながる大切な業務であり、出荷作業一つで、売上が大きく変わることもあります。
出荷作業において、まず何よりも重要なのが、受注した商品を正しく顧客の手元に届けることです。間違った商品を届けてしまえば、信頼を失い回復に時間を要します。最悪の場合、顧客を失ってしまう可能性もあります。次に注文を受注してから、顧客の手元に商品が届くまでのスピードです。配送予定日までにできる限り早く届ける必要があります。到着予定日よりも大幅に遅れてしまえば、顧客からの信頼を失ってしまいます。
しかし、正しい商品を、指定された日時に届けることができれば、顧客からの信頼獲得にもつながりますし、またミスが発生しなければ余計な業務も発生せず、出荷作業の生産性向上にもつながります。
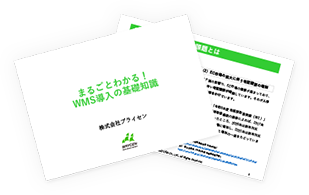
倉庫の出荷作業に欠かせない出荷指示
出荷指示とは、前述の出荷作業を実際に指示する業務を指します。出荷指示が出荷業務の正確性を左右するため、この出荷指示を正確に行うことが重要です。出荷指示では出荷する商品の種類、数量、出荷先の情報、出荷日時などが記載された出荷指示書を作成します。出荷指示書には以下のような内容が含まれています。
・商品情報:SKU(在庫管理単位)、商品名、数量など
・出荷先情報:顧客の名前、住所、連絡先など
・出荷条件:配送方法、指定日時、特別な取り扱い条件など
出荷指示のプロセスは、一般的に以下のステップで進んでいきます。
1. 受注確認
顧客からの注文が確認され、受注情報がシステムに登録されます。
2. 出荷指示書の発行
システムから出荷指示書が発行され、倉庫担当者に渡されます。この指示書には、出荷する商品の詳細情報が記載されています。
3. 出荷準備
倉庫担当者が出荷指示に基づいて商品をピッキングし、梱包します。
4. 配送手配
出荷指示書に基づいて、配送業者への引き渡しが行われます。
5. 出荷完了通知
出荷が完了したら、顧客に対して出荷完了の通知が行われます。
倉庫での出荷作業で発生しやすいミス
倉庫内で発生しやすいミスには以下の4つが考えられます。
・商品間違い
そもそもの商品間違いもありますが、色やサイズの間違いも発生しやすくなっています。目視での確認をする場合に発生しやすいミスとなります。
・商品数間違い
複数注文であったにもかかわらず、一つしか出荷しなかったなど商品数の見間違いで発生します。また大量に注文が入った際にも、数が多すぎて間違いに気づきにくいためミスが発生しやすいです。
・セット品の間違い
ギフトなどで、いくつかの商品を組み合わせて出荷する際に起こりやすいミスになります。定番の組み合わせであれば、間違いも起きにくいですが、イレギュラーな組み合わせなどの注文の場合は特に注意が必要です。
・発送先の間違い
発送作業のミスは商品を出荷する際に、発送伝票や、納品書の入れ間違い、見間違いにより発生する可能性があります。出荷担当者と、配送担当者でしっかりチェックし、発送作業の正確性を上げる必要があります。
出荷作業のミスを防止するには
出荷作業のミスは重大なクレームになりやすいため、極力ミスを減らす必要があります。
ここでは出荷作業のミス防止に役立つ方法をご紹介します。
・出荷作業のマニュアル作成
出荷作業の手順をマニュアル化する方法です。作業者によってやり方が違うと、システムを導入しても結局チェック不足でミスが起きる可能性があります。出荷作業のマニュアルを整備し、全員のやり方を統一することで、意識や手順を合わせることができます。また、マニュアル作成によって新人でも一定レベルの出荷作業がすぐにできるようになるので、早期育成、教育コストの削減にもつながります。
・システム導入
システムを導入して人的ミスを減らす方法です。人の目で確認していると、前述したような商品の取り間違いや、個数の数え間違いが発生してしまいます。WMSなどの倉庫管理システムを導入すれば、ピッキングする商品の位置情報が分かったり、バーコードをスキャンすることで商品情報が分かるので、取り間違いの防止に繋がります。
倉庫の出荷作業の流れ
お客様から受注を受けてから、お客様の元に配送するための発送作業までの間の業務が出荷作業です。
倉庫の出荷作業には、「出荷指示登録」から「積込/発送」までの、6つの作業があります。
出荷作業のミスを防止するためのマニュアル作成時には、この作業の流れをしっかりと把握していることが重要です。
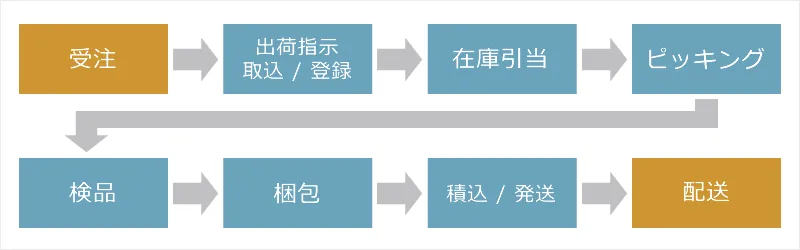
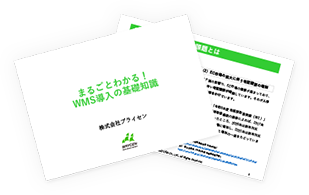
1.出荷指示・取込/登録
受注管理システムやEC(通販)サイトなど、上位システムで受注したデータを「倉庫管理システム(WMS)」に取り込み、管理画面から出荷登録を行います。
2.在庫引当
「倉庫管理システム(WMS)」で、在庫に対して出荷予約をします。
在庫引当をする上で重要なのは、同じ商品内において、引当済みの在庫に対して重複して引当をしないように注意することです。
在庫引当をすることにより、倉庫内の在庫数だけでなく、出荷予約がされていない在庫数がわかります。在庫が足りなくなった場合は、欠品扱いとなります。
【関連コラム】
在庫引当は倉庫管理システム(WMS)の肝となる機能!
3.ピッキング
出荷指示された商品を倉庫内から探し、取ってくる作業になります。
「倉庫管理システム(WMS)」からピッキングリストを出力し、記載されている棚から該当の商品を指示の数だけ取ってきます。
ピッキングの方法には大きく分けて、2つの方法があります。
・オーダーピッキング(摘み取り方式)
出荷指示の単位で取ってくる方式です。 ピッキング対象は全ロケーションになりますが、作業者は1人で完結します。
1伝票単位でみると、出荷が早い、出荷指示の内容変更にも対応しやすい、といったメリットがありますが、ピッキング回数はトータルピッッキング(下に記載)よりも多くなるため、伝票数が多いと非効率な点でデメリットになることがあります。
・トータルピッキング (種まき方式)
商品の単位で取ってくる方式です。
作業を分担しやすいため、各作業者が担当するエリア・ロケーション内のみの作業となります。取ってきた後は、各伝票ごとに振り分ける「仕分け」作業もあります。
ピッキング回数が少ないことがメリットで、特に同じ商品の組み合わせが多いときに効果を発揮します。しかし、作業者全員が終了するまで完了とならなかったり、同じ商品の組み合わせが少ない場合は、仕分け作業に時間がかかる点がデメリットになります。
4.検品
ピッキングした商品、数量が合っていること、さらにキズなどの不備が無いかを確認する作業です。検品の方法も大きくわけて、2つの方法があります。
・バーコード検品
ハンディターミナルを使用して商品のバーコードをスキャン、出荷指示と突合します。現物との突合せのため、商品が正しいか、出荷数量の過不足がないかを正確に判断できます。
しかし、商品にバーコードがない場合は、商品のJANコードなどを毎回入力しなくてはならないため、作業効率が悪くなります。ほぼ全ての商品にバーコードがある場合には便利です。
【関連コラム】
ハンディターミナルで倉庫作業しよう!
・リスト検品
納品書やピッキングリスト等と現物とで、人の目による確認をします。
バーコードがない商品が多い場合、出荷数量が少ない場合は、作業時間が短縮できます。しかし、人の目による確認のため正確性に欠けてしまいます。
この検品が最終的なチェックであり、この作業ミスが出荷ミスに直結します。品質を保証する上で、最も重要な作業になります。
5.梱包
商品を適切な材料、外箱に入れる作業です。外箱に対してシュリンク(透明なフィルムで覆うこと)したり、ギフト用に包装しなおすことなどをします。
また、梱包する際に下のマークのような、積込時、配送時の注意事項をシールで張る作業もあります。
ここできちんと梱包されていないと、配送時に商品にキズがついてしまい、クレームに繋がってしまいます。
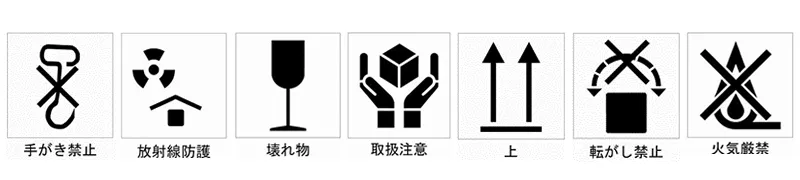
6.積込/発送
運送業者が手配したトラックに梱包した商品を入れる作業です。この発送作業が完了した時点で、倉庫内での出荷作業が完了したことになります。
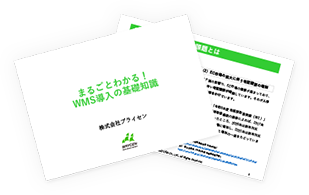
さいごに
これだけの作業を毎日、手作業だけで行い、管理していくことはとても大変な作業です。また、人的ミスも多くなります。「倉庫管理システム(WMS)」を有効活用することで、正確性や効率化を図ることが重要です。
次回は、各業務における課題やその解決方法などをご紹介いたします。